What are Hermetic Seals?
The first hermetic seal is said to have been created by the Greek god Hermes who invented a process of creating airtight glass tubes, according to Greek mythology. Regardless of the origins of hermetic sealing, it is still an important technology that is used abundantly today. Hermetic sealing is the process of creating an airtight seal that prevents gases, liquids, and solids from passing through. There are many distinct types of hermetic seals, and they can have a wide variety of purposes depending upon the application it is being used for.
In electronics, there are applications in which one housing or enclosure may need to be isolated from another. However, there also tends to be a requirement for power and electrical signals to pass between the two, which is usually accomplished with connectors. The connector can create a vulnerability in the isolation between the two enclosures allowing moisture and gases to leak through. For many applications it is imperative that connectors are specifically designed to create a hermetic seal to prevent any leakage.
An extreme example of where hermetically sealed connectors are required is in Chemical Vapor Deposition (CVD) ovens. The connectors must prevent contaminating gases from penetrating through the assembly. This allows systems to operate in controlled environmental conditions required for the batch processing. In addition, the connectors must be able to withstand the extreme temperature variations, intense vibration, and other physical factors that can accompany industrial processing. Failure of a seal can be catastrophic to the batch and the system.
Types of Hermetic Seals
Several types of hermetic seals exist. These include glass seals (matched seal), compression seals, and epoxy seals.
Matched seals are the most common type of hermetic seals and offer an economical, low-cost, and light duty seal. In matched seals, glass offers a rigid shape that metal can compress and bond against while also providing support for contacts. These matched seals are only possible if the glass and metal have the similar coefficients of thermal expansion.
On the other hand, compression seals offer a more robust seal for more demanding applications. These seals may have differing coefficients of thermal expansion but can operate reliably in high-pressure applications. These are the most expensive and often require custom molds and fixtures to accomplish.
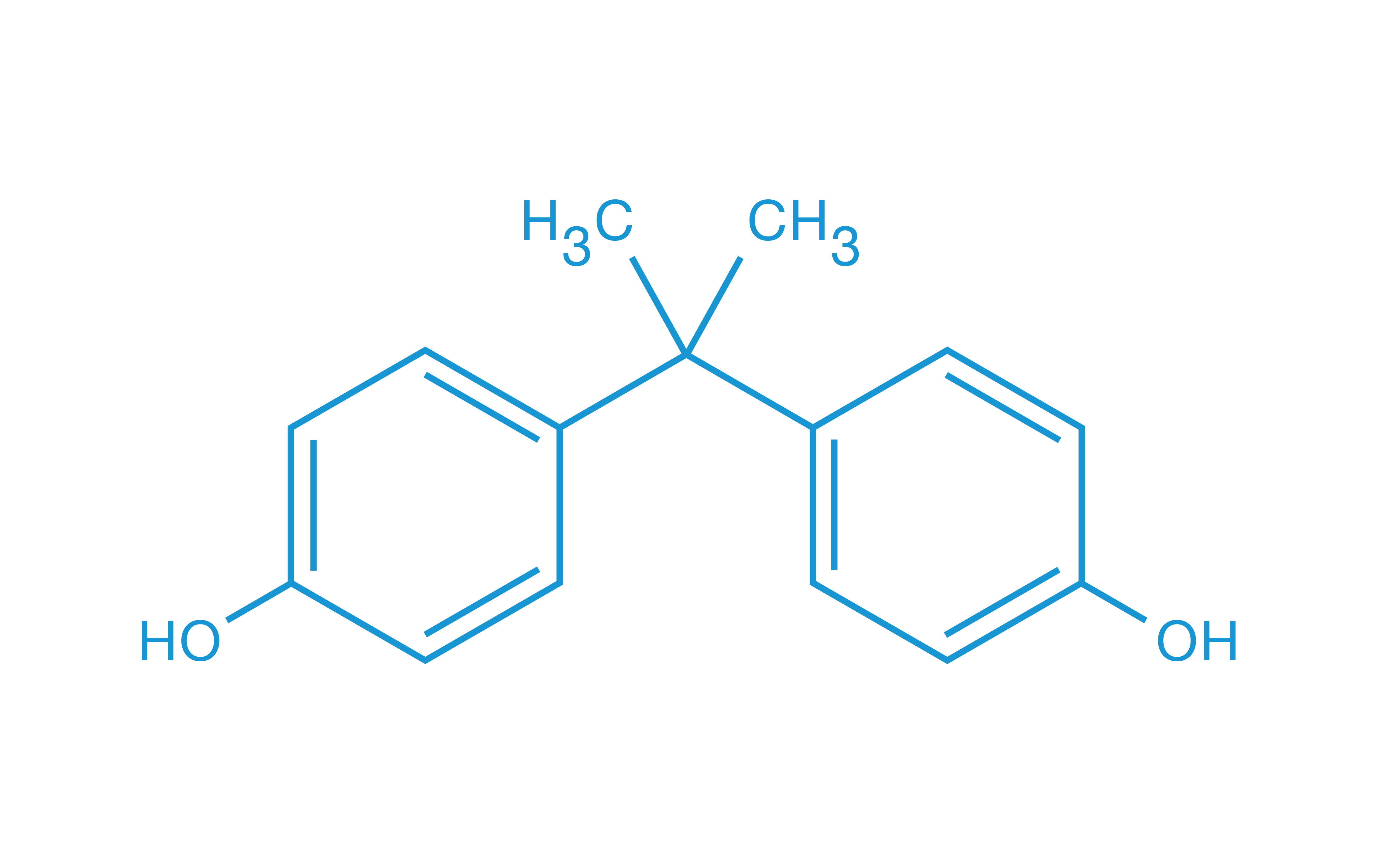
Figure 1: Epoxy stabilizer dimethyl-dihydroxy benzene (C8H10O2)
Lastly, epoxy seals offer a great alternative method of hermetic sealing. It bonds well to metals, has a high dielectric strength, good thermal conductivity, and offers great resistance to corrosive materials. The advantages of using an epoxy seal are:
- Strong polar attraction – Epoxies form a strong bond to the oxides of metal surface preventing leakage of gases or fluids in low and high-pressure conditions.
- High dielectric strength – Epoxy can withstand high voltage without breaking down, enabling higher signal density.
- Good thermal conductivity – Epoxy will transfer heat away from component and reduce overheating and thermal degradation.
- Wide chemical resistance – Epoxy is inert to most chemicals; therefore, it is less corrosive and more durable.
Hermetic Seal Testing and Performance
The performance of a hermetically sealed connector is often evaluated by its leak rate, which is measured in units of cubic centimeters per second [cm3/sec]. This is a measure of the volume of gas that will pass through a seal over time.
Depending upon a given application, different requirements will be needed for a hermetic seal. For example, a hermetic seal on a medical device may be expected to have a much longer lifetime and better performance than a seal used on a piece of industrial equipment.
Connector seal performance can be categorized based on leak rates given below:
- Lower performing seals = 10-4cm3/s
- High quality seals = 10-8cm3/s
- Highest-performance seals = 10-12cm3/s
There are several test methods used to measure leak rate, three of which are listed below:
Pressure decay method
The pressure decay method is a low-cost technique to assess lower performance devices. This test is performed by trapping pressure inside of a product and then measuring the pressure loss.
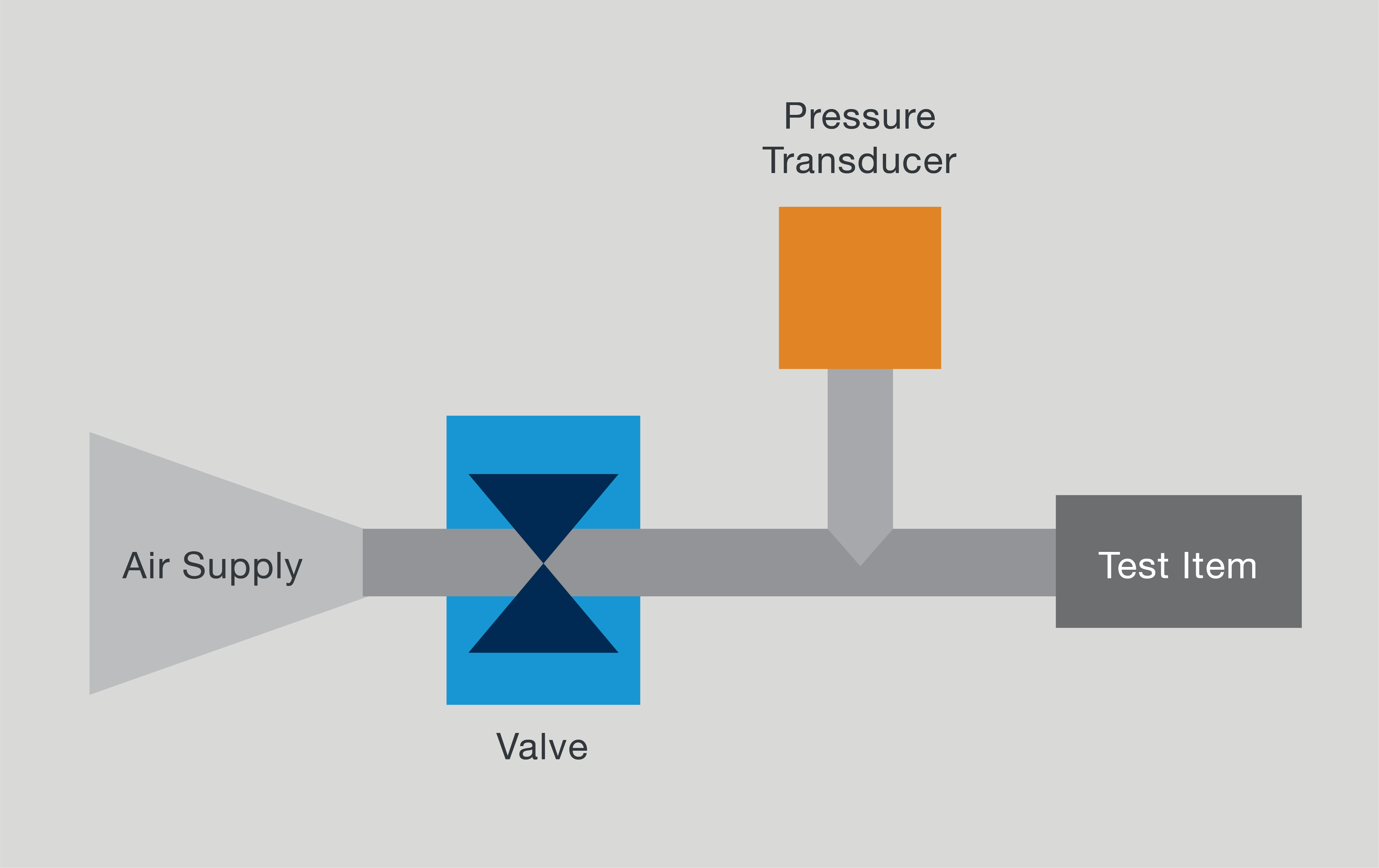
Figure 2: Pressure decay method diagram
Mass spectrometry method
On the other hand, the mass spectrometry method is costly but offers the best method for accurate, high-performance testing. In this test, gases are ionized in a vacuum, usually Helium. A voltage is applied which accelerates the ions of Helium and consequently creates a magnetic field. The mass spectrometer can measure the current the ions create and measure the leakage through its direct proportionality to the Helium concentration in the vacuum.
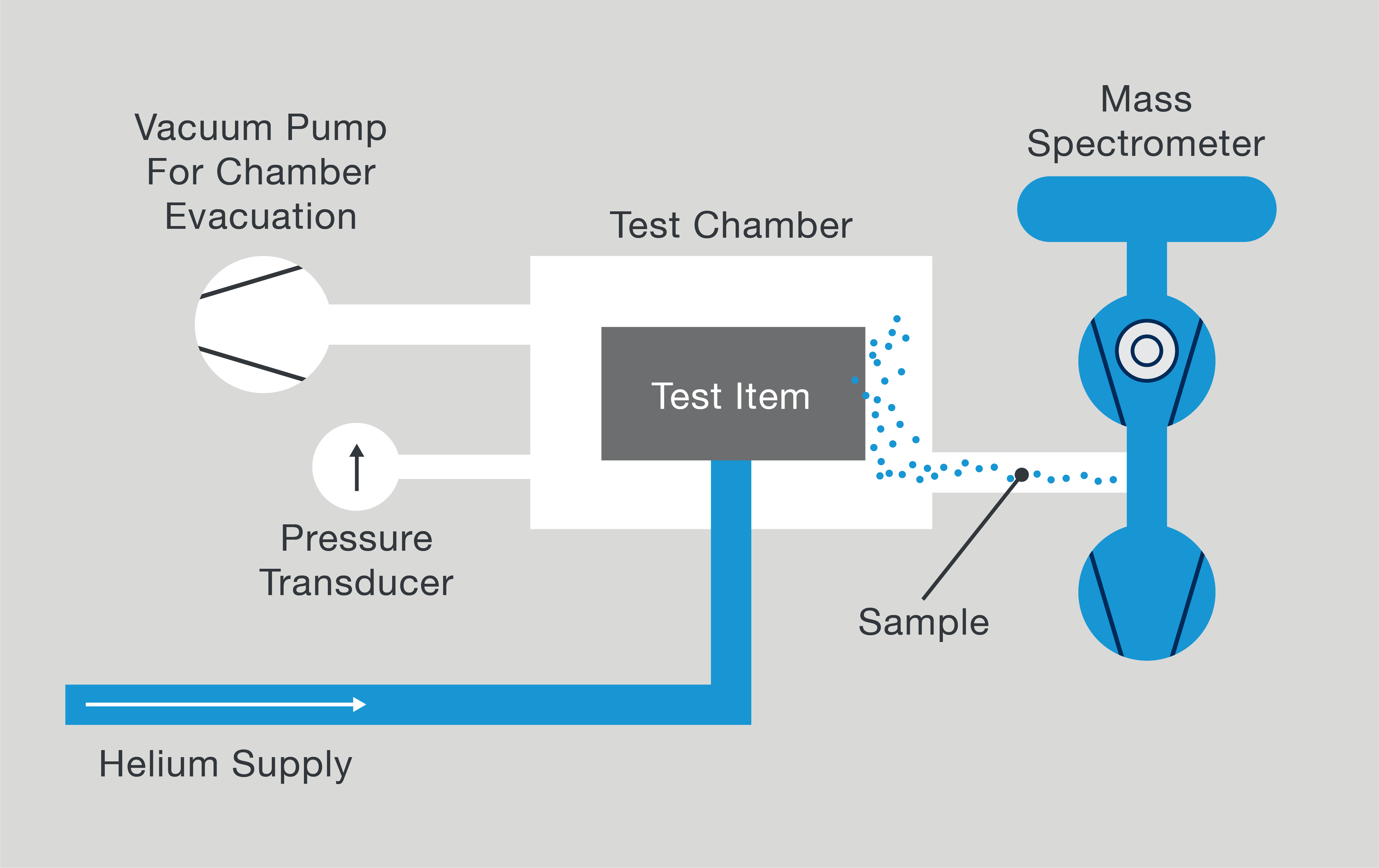
Figure 3: Mass spectrometry method diagram
Tracer gas method
Lastly, the tracer gas method offers a tradeoff between the two. It is less costly than mass spectrometry but more accurate than the pressure decay method. This test method is accomplished by measuring the concentrations of a tracer gas (again usually Helium) in an enclosed chamber.
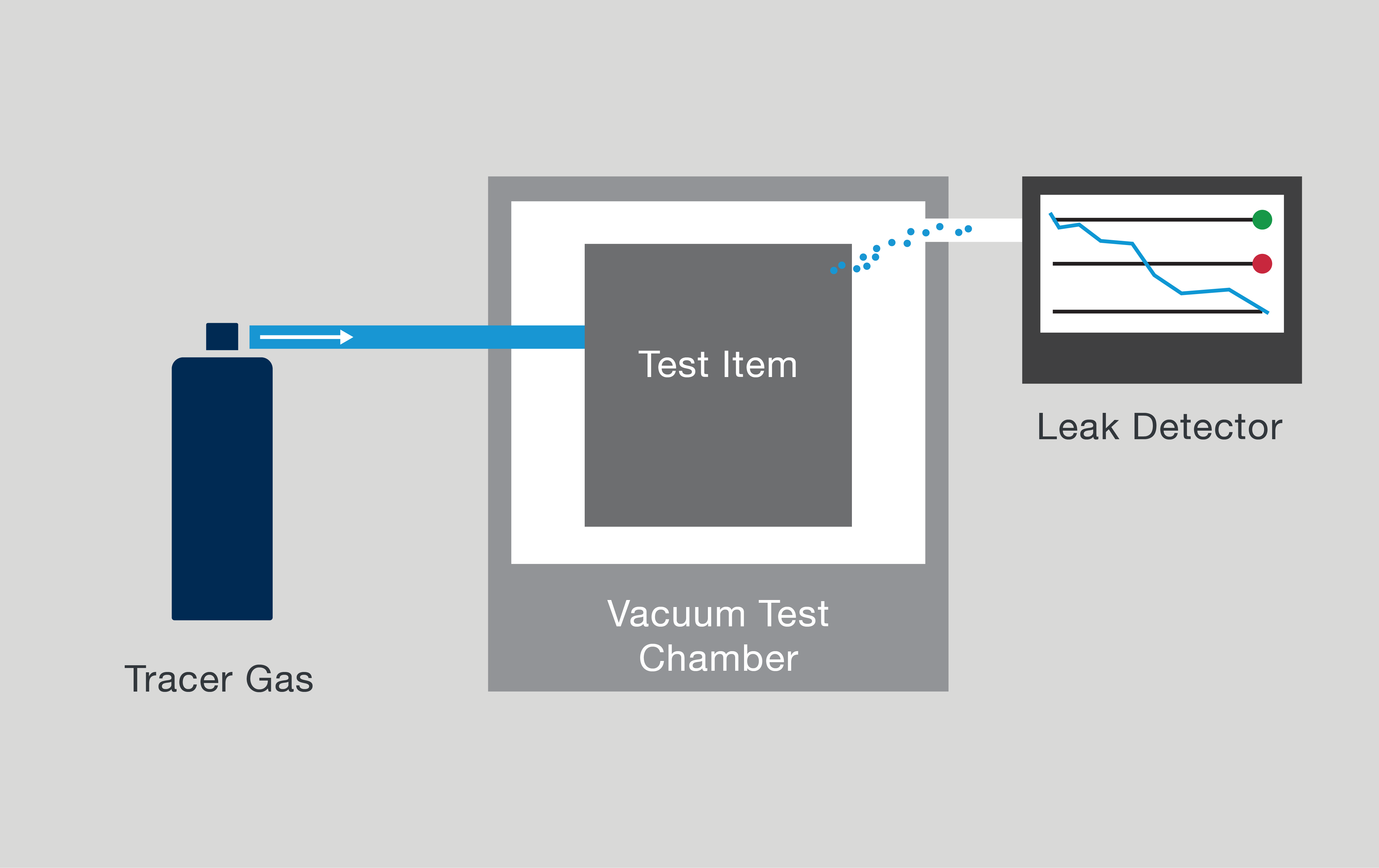
Figure 4: Tracer gas method diagram
Hermetically Sealed Connectors
Many electrical connectors are hermetically sealed using epoxy. It allows for a cost-effective and easy-to-manufacture method of hermetically sealing connectors. Cinch offers a wide variety of hermetically sealed connectors and has developed a proprietary epoxy that creates high-performance hermetic seals in comparison to alternative solutions.
Some of the options available from Cinch include the following:- Dual Lobe Nano-Miniature Connectors
- Aluminum Weldable Stabilizer Series, RF Feedthroughs
- UHV Vacuum Products
- Micro-D Dura-Con Hermetic Connectors
- Micro-D Connectors with Ceramic Dielectric Material
The micro-D connectors, as well as alternative hermetically sealed options, are all available as off-the-shelf components. These can be found through common distributors such as Mouser and Digi-Key and are well-stocked.
Furthermore, custom solutions are also available. If off-the-shelf connectors are not suitable for a given application, Cinch can collaborate with customers to provide custom connector options with hermetic seals. Custom solutions can be delivered as complete assemblies and capabilities for custom solutions can go as far as building a connector into an enclosure.
Hermetic Connectors for Rugged Applications
Overall, hermetic seals can come in a variety of shapes, forms, and sizes. The application and the needed performance from the seal will often dictate the type of hermetic seal that is used. Hermetic seals are often fabricated using an epoxy seal and can achieve very minimal leak rates on the order of 10-8cm3/s.
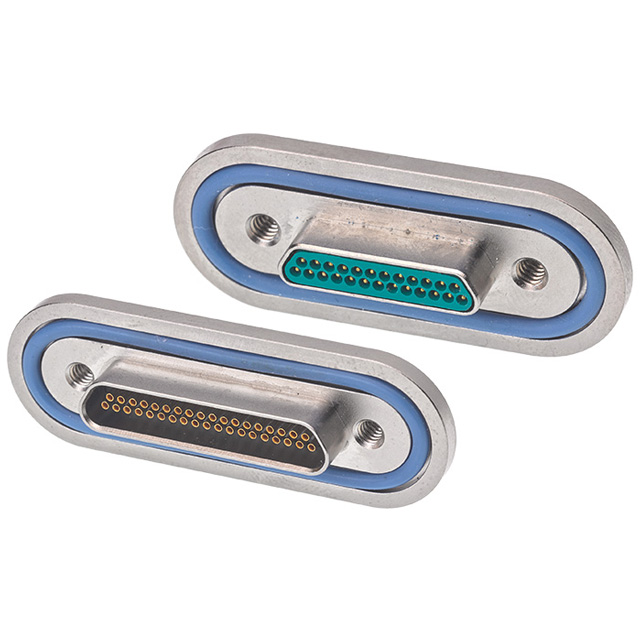
Figure 5: Cinch hermetically sealed micro-D connectors
For quick prototyping and testing needs, many of the hermetically sealed connectors from Cinch are readily available as off-the-shelf components. On the other hand, for the more unique applications, contact Cinch directly to create custom solutions for the most demanding applications.